Heat Treatments
As a general definition, heat treatment is a series of heating and cooling operations applied to the material to arrange its hardness, grain structure, and mechanical properties to the desired levels.
Considering the type of heat-treating process and the material properties to be improved, heat treatment is commonly categorized into two groups: annealing and hardening.
Annealing

As a heat treatment process, annealing is carried out to improve the machinability and plastic forming capacity of the material by improving its physical properties. In this process, the material is first heated up to a certain temperature, then it is exposed to controlled cooling.
The annealing process is called variously based on the operational temperatures and cooling modes used. Major annealing operations are defined as follows:
- Stress – Relief Annealing
- Recrystallization Annealing
- Normalization Annealing
- Softening Annealing
-
Stress-Relief Annealing: The inner stresses of the material may increase in various directions due to being subjected to operations such as extreme heating, sudden cooling, or plastic forming. In order to relieve the inner stresses, the workpieces are exposed to temperatures above the maximum operating temperature and below the phase transformation temperature for the period of maximum two hours.
-
Recrystallization Annealing: The workpieces that are shaped using plastic forming methods experience permanent structural alterations in their grain structures, particularly at the walls of the material. Therefore, the hardness and strength of the material increase while its ductility and electrical conductivity decrease. In the process of recrystallization annealing, the material is exposed to heat below phase transformation temperature for a period of up to an hour to obtain a grain structure of the smooth and regular form. As a result, its pre-deformation properties are recovered. Recrystallization annealing is also called recrystallization.
-
Normalization Annealing: Although the materials obtain positive properties by all kinds of annealing processes, annealing leads to grain coarsening in the materials. The process of normalization annealing is carried out to avoid coarse grain structure which is not desired in terms of the machinability of the material. In normalization annealing, the workpiece is heated up to the hardening temperature of its material, then it is left for cooling down in the air under calm weather conditions. Cooling in the air is the distinct characteristic of normalization annealing since the material is exposed to instant cooling rather than slow controlled cooling. As a result, a finer grain structure is achieved. Normalization annealing is also called normalization.
-
Softening Annealing: Hardness value is a critical property for the machinability of the material. The materials that are not subjected to heat treatment show different hardness values at room temperature based on their carbon contents. The minimum hardness value is desired for the materials particularly for the operations of plastic deformation. Therefore, the materials are subjected to softening annealing to achieve lower levels of hardness values.
The steel material has a granular structure at room temperature. Also, in direct proportion to the carbon content, it has a form of sequential carbide precipitation in the form of thin long plates. The intensity of these carbide plates in this structure, which is called perlite, leads to an increase in the carbon content of the material. As a result, the hardness value of the material increases.
Carbide plates of a thin and long structure are turned into a shorter and spheroidal structure by softening annealing. Thus, the steel gets a softer structure that can be easily formed compared to its original form. This method is also known as spheroidization annealing.
Hardening
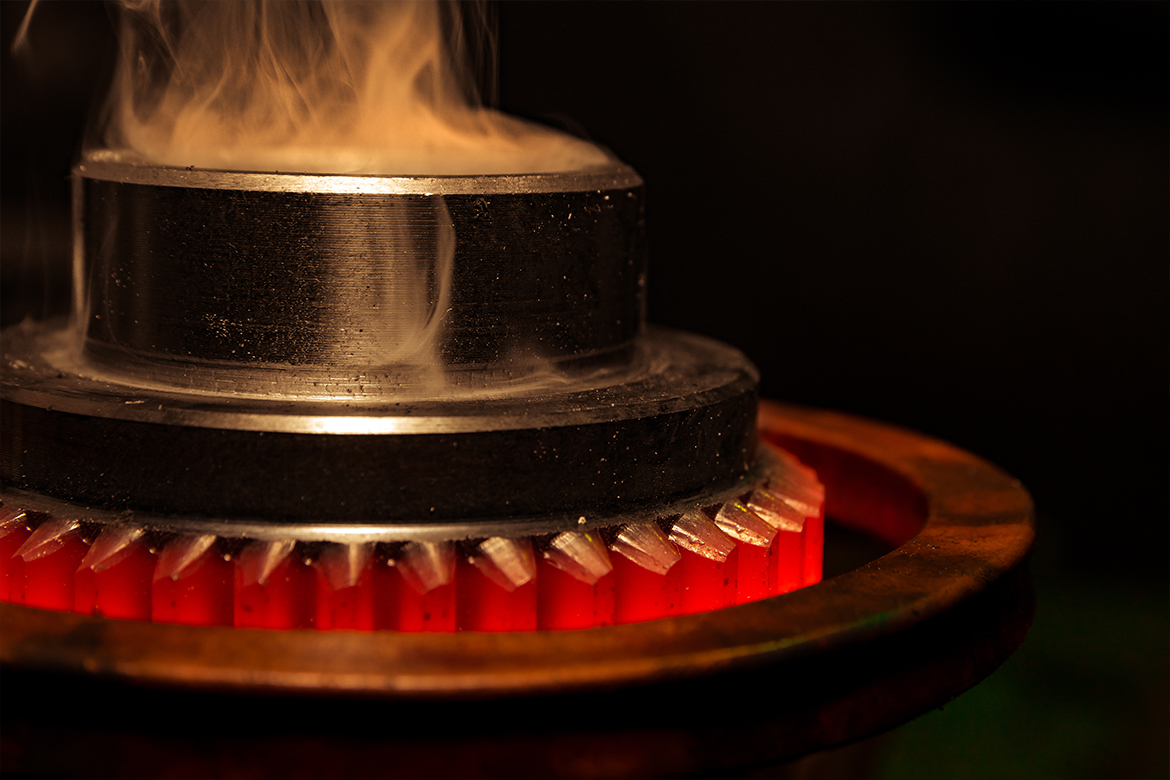
It might be required to increase the hardness of the whole workpiece or a part of it up to the core or only along the wall surface by evaluating the operating conditions of the manufactured material. Therefore, different heat treatment methods may be applied to the workpiece according to the intended feature. The hardening process is carried out using different methods taking into consideration the application method and the properties of the intended structure.
Heat Treating: In this process, the material is subjected to quenching and tempering operations to obtain the intended hardness value and mechanical properties. This process is particularly suitable when the entire cross-section of the workpiece is to be hardened.
The quenching process can be simply described as hardening the material by heating it up to the hardening temperature and cooling it instantly. In this process, factors such as the selection of the hardening temperature, heating rate, cooling medium, and cooling rate, and the correlation between these factors should be determined accurately, which requires expertise in this process.
The range of hardening temperature for the material is determined by a series of experiments so as to achieve maximum hardness with the smallest grain size. The heating process performed below or above these values will lead to a low hardness value or failure to achieve the intended internal structure. Besides, holding the material at hardening temperature for the proper period (holding time) is another important factor, and it is related to the fact that the material is an alloy, low alloy, and its grain size.
In heat treatment, the quenching medium is selected taking into consideration the alloy content of the material. While water and salt baths are preferred as a quenching medium for low alloy steels, a soft medium such as oil is preferred for high alloy steels considering the risk of distortion. Water, oil, salt bath, and air are widely used as a cooling medium.
-
Water: One of the most important parameters in the water quenching process is the temperature of the water which is used as cooling media to cool the hot workpiece. The water temperature between 20°C and 40°C is ideal for this process. At temperatures above 60°C, the cooling rate decreases significantly.
-
Oil: The cooling rate of the oil is slower than that of the water in the quenching process. The oil temperature between 50°C and 80°C is ideal for this process. Also, stirring the oil rapidly and continuously increases the efficiency of the process greatly.
-
Brine Cooling: To increase the efficiency of the water quenching process, sodium hydroxide or common salt can be added to the water. The common salt is rarely preferred because it causes corrosion on the workpiece. The cooling rate can be increased significantly by adding 10% NaOH into the cooling medium. This type of usage also increases the high hardening depth and provides low internal stresses.
-
Air: Since the cooling rate of air is very low, the air is the least efficient quenching medium compared to other quenching media. In fact, the cooling rate of air under calm weather conditions is less than 1% of that of the water. For this reason, this method can only be preferred for high-speed steels.
Tempering
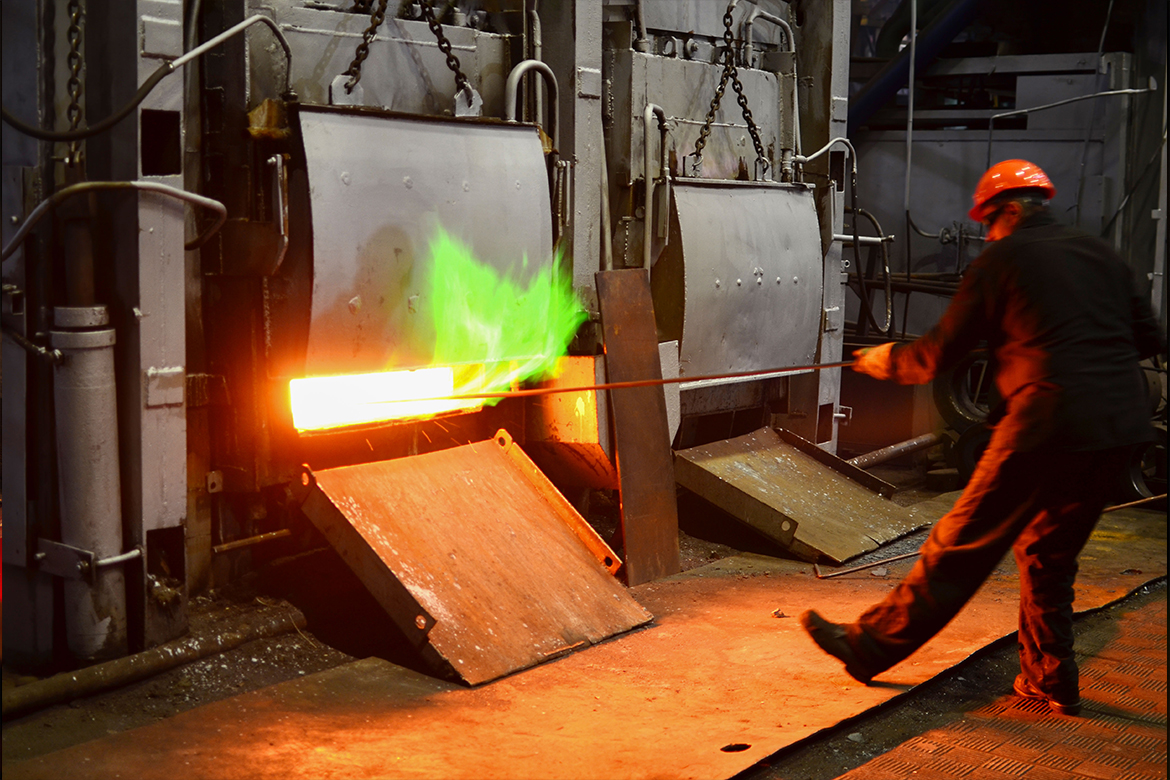
The material has a very rigid and fragile final structure after the quenching process and internal stresses occur during instant cooling. Therefore, in the tempering process, the material is heated again, kept at the same temperature for a certain period, and cooled down to improve its toughness.
Tempering process can be performed at different temperatures depending on the desired toughness rate, hardness value, and final structure. Tempering a workpiece that is completely cooled down after the quenching process may cause cracking. For this reason, tempering should be carried out immediately when the temperature of the workpiece drops to a range between 60°C-80°C.
Case Hardening
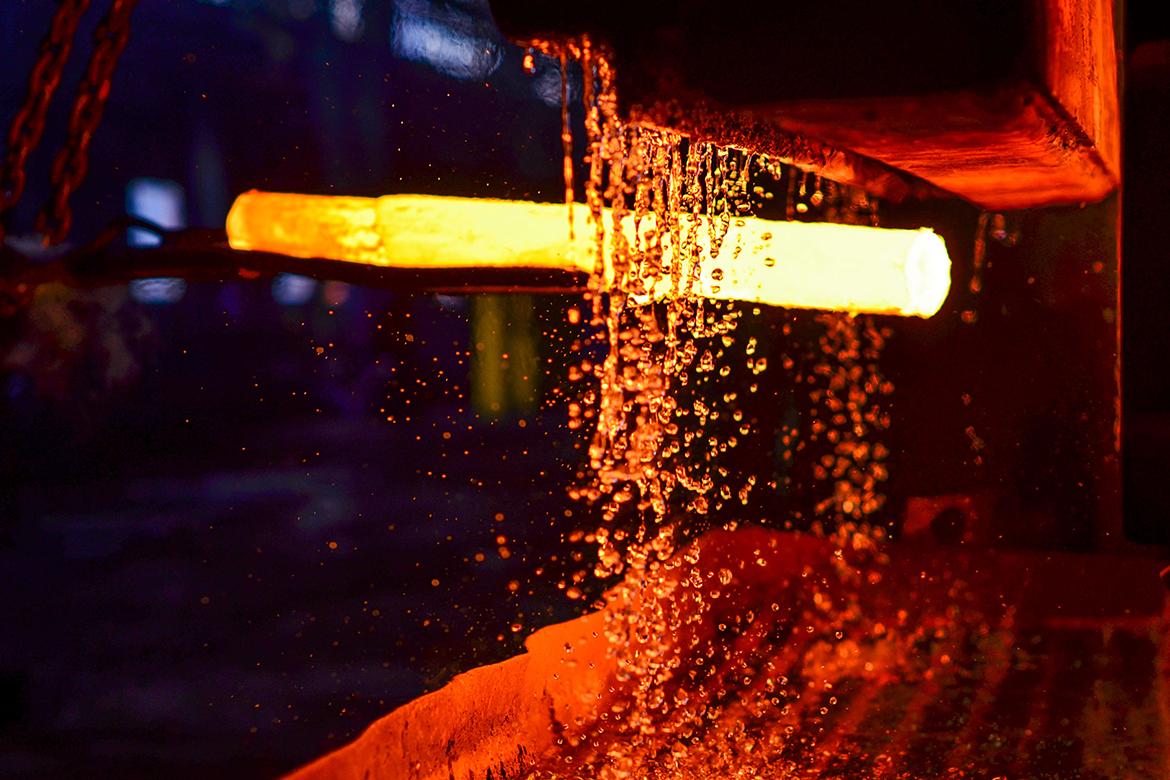
The machinability of low carbon steel materials is very high. Therefore, they are subjected to the hardening process by infusing additional carbon following the machining process taking into consideration their intended uses. This operation increases the wear resistance of the workpiece’s surface. It also provides required toughness and high impact strength to the entire workpiece while keeping the core area soft.
The case hardening process can be performed in a medium of the solid, liquid, or gas phase. Case hardening in the gas medium is ideal in that it is economic and the easiest method to control. The hydrocarbons such as CO or coal gas, etc. are used as the carbonizing medium. The carbonizing salts such as sodium cyanide and potassium cyanide, etc. are widely used in the processes of case hardening with a liquid carbonizing medium. The liquid medium is usually preferred for the case hardening process of small workpieces. On the other hand, charcoal is widely used as a solid medium in case hardening processes. Since this method is complicated and hard to control, it requires expertise.
The aim of the case hardening process is to increase the carbon rate of the surface of the workpiece by 0,7-0,8%. Infusion of carbon above this range leads to carbide precipitation and results in a fragile surface. The critical factor in the case hardening process is determining the effective case depth.
The workpiece is subjected to a quenching process following the carbon infusion process, thus, the wall of the workpiece is hardened. The quenching process is carried out by quenching from the carbon infusion temperature (direct quenching), cooling down to room temperature and treating (single quenching), or treating at low temperature after quenching from carbon infusion temperature. Tempering must be carried out after the quenching process. The highest wear resistance after the case hardening process can be achieved by tempering at about 300°C rather than at the highest hardness value.
Induction Hardening
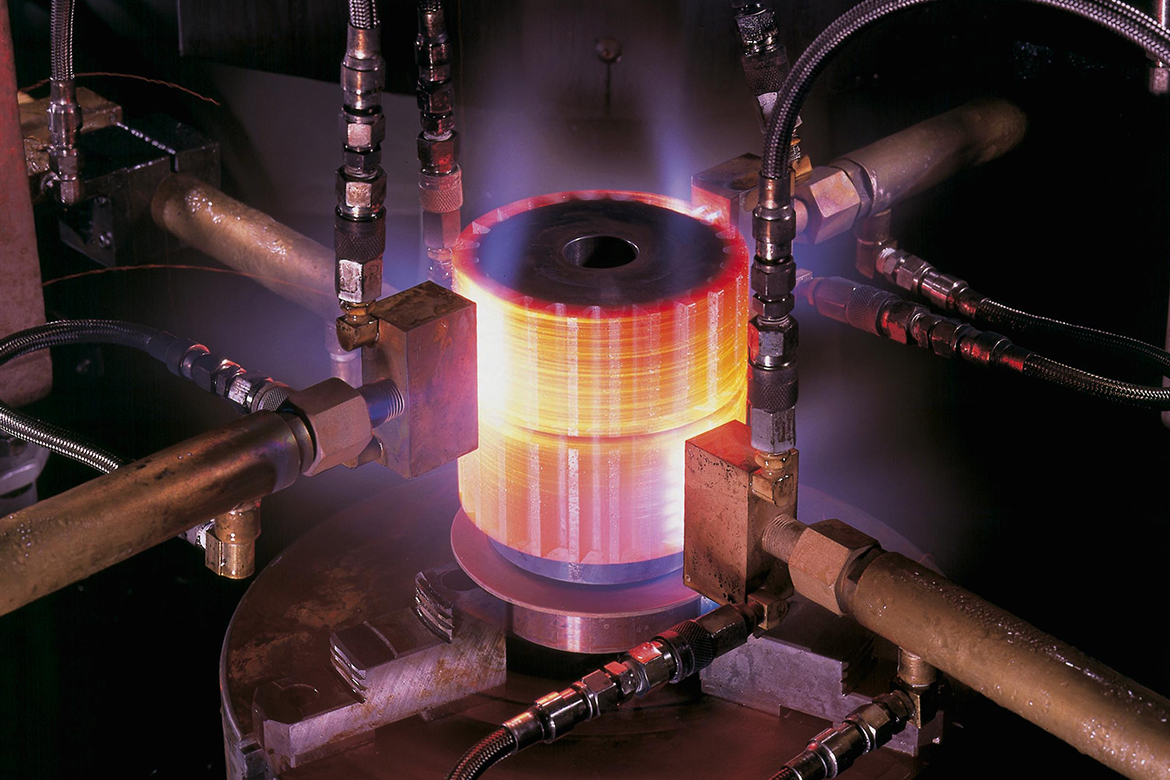
As a surface hardening process, induction hardening can be defined as instantly heating the surface of the workpiece utilizing induced electrical currents and then cooling it instantly by quenching. Although the method is similar to flame hardening, induction hardening provides advantages in terms of its efficiency considering the process duration and high thermal accumulation on the surface of the workpiece. Usually, upon instant heating of the workpiece utilizing induced currents, it is instantly cooled in water as a cooling medium. Therefore, the risk of cracking in the workpiece increases in high carbon steels. However, if the temperature of the cooling medium (water) is about 60˚C or if common salt is used as an addition, the risk of cracking and inner stress can be eliminated.
In order to avoid internal stresses, the tempering process is carried out at the temperature between 150˚C and 200˚C after the hardening process.
We want to make our websites more user-friendly and continuously improve them. If you continue to use the websites, you agree to the use of cookies. OK For further information, please refer to our cookie policy...