Trattamenti Termici
Per definizione generale, il trattamento termico consiste in una serie di operazioni di riscaldamento e di raffreddamento applicate al materiale per regolarne la durezza, la struttura dei grani e le proprietà meccaniche ai livelli desiderati.
Considerando il tipo di processo di trattamento termico e le proprietà del materiale da migliorare, questo processo viene comunemente classificato in due gruppi: ricottura e tempra.
Ricottura

Come trattamento termico, la ricottura viene effettuata per migliorare la lavorabilità meccanica e la capacità di plastificazione del materiale, migliorandone le proprietà fisiche. In questo processo, il materiale viene prima riscaldato fino ad una certa temperatura e poi esposto ad un raffreddamento controllato.
Il processo di ricottura viene chiamato in vari modi in base alle temperature di esercizio e alle modalità di raffreddamento utilizzate. Le principali operazioni di ricottura sono definite come segue:
- Ricottura di distensione
- Ricottura di ricristallizzazione
- Ricottura di normalizzazione
- Ricottura di addolcimento
-
Ricottura di distensione: le sollecitazioni interne del materiale possono subire variazioni a causa di operazioni come il riscaldamento estremo, il raffreddamento improvviso o la formazione di plastica. Al fine di alleviare le tensioni interne, i pezzi in lavorazione sono esposti a temperature superiori alla temperatura massima di esercizio e inferiori alla temperatura di trasformazione di fase per un periodo di massimo due ore.
-
Ricottura di ricristallizzazione: I pezzi che vengono modellati con metodi di formatura plastica subiscono alterazioni strutturali permanenti nella loro struttura granulometrica, in particolare sulle pareti del materiale. Di conseguenza, la durezza e la resistenza del materiale aumentano mentre la sua duttilità e la conducibilità elettrica diminuiscono. Nel processo di ricottura di ricristallizzazione, il materiale viene esposto al calore al di sotto della temperatura di trasformazione di fase per un periodo fino ad un'ora per ottenere una struttura granulometrica regolare e liscia. Di conseguenza, le sue proprietà precedenti alla deformazione vengono recuperate. La ricottura di ricristallizzazione è anche chiamata ricristallizzazione.
-
Ricottura di normalizzazione: anche se i materiali acquisiscono proprietà positive da tutti i tipi di processi di ricottura, questa porta alla formazione di grani più grossi nei materiali. Il processo di ricottura di normalizzazione viene effettuato per impedire la formazione di una struttura a grana grossa che risulta indesiderata dal punto di vista della lavorabilità del materiale. Nella ricottura di normalizzazione, il pezzo viene riscaldato fino alla temperatura di indurimento del suo materiale, poi viene lasciato raffreddare all'aria in condizioni di temperatura stabile. Il raffreddamento in aria rappresenta la caratteristica distintiva della ricottura di normalizzazione, in quanto il materiale è esposto a un raffreddamento istantaneo piuttosto che a un raffreddamento lento e controllato. Di conseguenza, si ottiene una struttura a grana più fine. La ricottura di normalizzazione è anche chiamata normalizzazione.
-
Ricottura di addolcimento: la durezza è una proprietà critica per la lavorabilità del materiale. I materiali che non sono sottoposti a trattamento termico mostrano valori di durezza differenti a temperatura ambiente in base al loro contenuto di carbonio. Per i materiali si auspica un valore minimo di durezza, in particolare per le operazioni di deformazione plastica. Pertanto, i materiali sono sottoposti a ricottura di addolcimento per ottenere valori di durezza più bassi.
A temperatura ambiente, un materiale d'acciaio ha una struttura granulare. Inoltre, presenta una forma di precipitazione sequenziale di carburo sotto forma di sottili piastre lunghe, direttamente proporzionale al contenuto di carbonio. L'intensità di queste piastre di carburo in questa,struttura chiamata perlite, porta ad un aumento del contenuto di carbonio del materiale. Di conseguenza, la durezza del materiale aumenta.
Le piastre di carburo di una struttura sottile e lunga vengono trasformate in una struttura più corta e sferoidale, mediante la ricottura di addolcimento. In questo modo, l'acciaio ottiene una struttura più morbida che può essere facilmente modellata rispetto alla sua struttura originale. Questo metodo è noto anche come ricottura di sferoidizzazione.
Indurimento
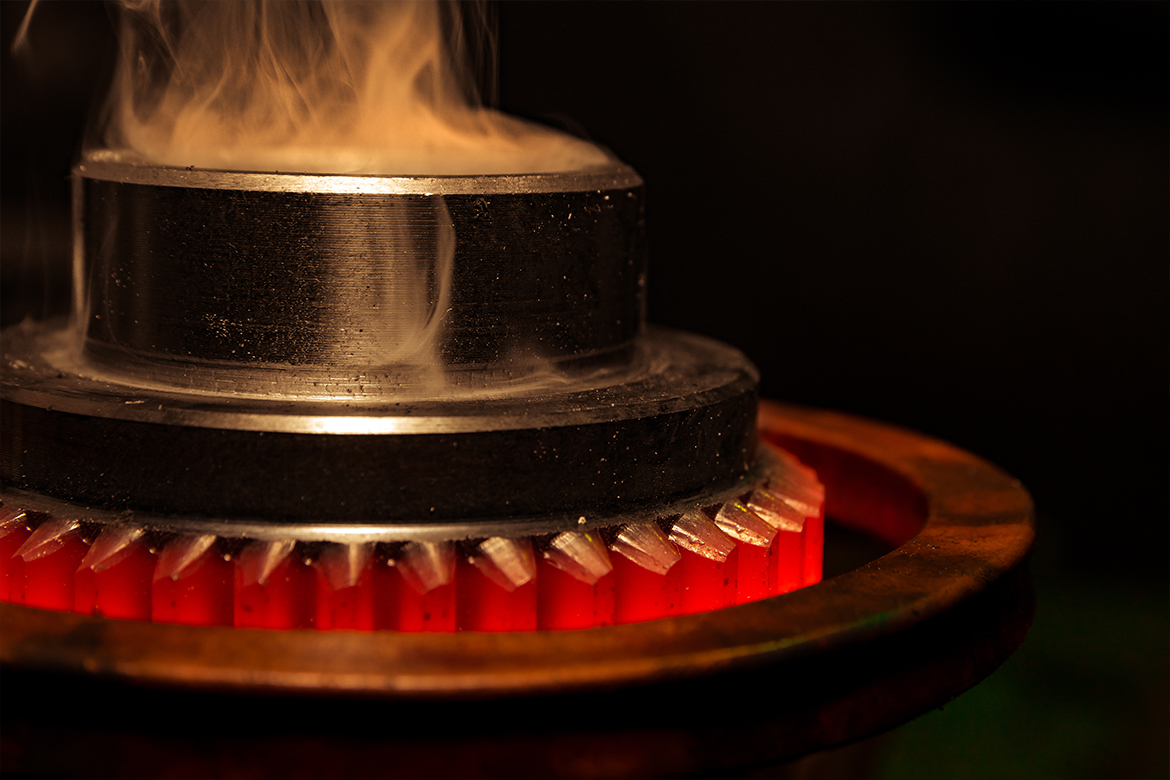
Potrebbe essere necessario aumentare la durezza dell'intero pezzo o di una parte di esso fino al nucleo o solo lungo la superficie della parete in base alla valutazione delle condizioni operative del materiale. Pertanto, possono essere applicati al pezzo in lavorazione metodi di trattamento termico diversi a seconda della caratteristica desiderata. Il processo di indurimento viene effettuato con diversi metodi tenendo conto delle caratteristiche della struttura desiderata e del tipo di applicazione.
Trattamento termico: In questo processo, il materiale viene sottoposto a operazioni di tempra e rinvenimento per ottenere il valore di durezza e le proprietà meccaniche desiderate. Questo processo è particolarmente adatto quando si deve temprare l'intera sezione trasversale del pezzo.
Il processo di tempra può essere descritto semplicemente come l'indurimento del materiale, riscaldandolo fino alla temperatura di tempra e raffreddandolo istantaneamente. In questo processo è richiesta molta competenza dato che fattori come la selezione della temperatura di tempra, la velocità di riscaldamento, il mezzo di raffreddamento, la velocità di raffreddamento e la correlazione tra questi fattori devono essere determinati con precisione.
L'intervallo di temperatura di tempra del materiale viene determinato attraverso una serie di esperimenti che hanno lo scopo di ricavare la massima durezza con la più piccola granulometria. Il processo di riscaldamento eseguito al di sotto o al di sopra di questi valori porterà ad un basso valore di durezza o al mancato raggiungimento della struttura interna desiderata. Un altro fattore importante è il mantenimento del materiale alla temperatura di tempra per il periodo adeguato (tempo di tenuta), ed è legato alla natura della lega e alla sua granulometria.
Nel trattamento termico, il materiale utilizzato per la tempra viene selezionato tenendo conto del contenuto di lega del materiale. Per gli acciai a bassa lega si preferiscono i bagni di acqua e sale come mezzo di tempra, mentre per gli acciai ad alta lega si preferisce un mezzo morbido come l'olio, in considerazione del rischio di distorsione. Sono ampiamente utilizzati come mezzo di raffreddamento l'acqua, l'olio, il bagno di sale e l'aria.
-
Acqua: uno dei parametri più importanti nel processo di tempra in acqua è la temperatura dell'acqua che viene utilizzata come mezzo di raffreddamento del pezzo caldo. Una temperatura dell'acqua compresa tra 20 ° C e 40 ° C è ideale per questo processo. A temperature superiori a 60 ° C, la velocità di raffreddamento diminuisce notevolmente.
-
Olio: La velocità di raffreddamento dell'olio è più lenta di quella dell'acqua nel processo di tempra. Una temperatura dell'olio compresa tra 50 ° C e 80 ° C è ideale per questo processo. Inoltre, agitare l'olio rapidamente e continuamente aumenta l'efficienza del Processo notevolmente.
-
Raffreddamento in salamoia: per aumentare l'efficienza del processo di raffreddamento in acqua, si può aggiungere idrossido di sodio o sale comune. Il sale comune difficilmente viene preferito perché causa la corrosione del pezzo in lavorazione. La velocità di raffreddamento può essere aumentata significativamente aggiungendo nel mezzo di raffreddamento il 10% di NaOH. Questo tipo di applicazione aumenta inoltre la profondità di tempra e causa basse sollecitazioni interne.
-
Aria: poiché la velocità di raffreddamento dell'aria è molto bassa, questa costituisce il mezzo di raffreddamento meno efficiente rispetto agli altri mezzi di raffreddamento. Infatti, la velocità di raffreddamento dell'aria in condizioni di calma atmosferica è inferiore all'1 % rispetto a quella dell'acqua. Per questo motivo, questo metodo può essere preferito solo per gli acciai rapidi.
Rinvenimento
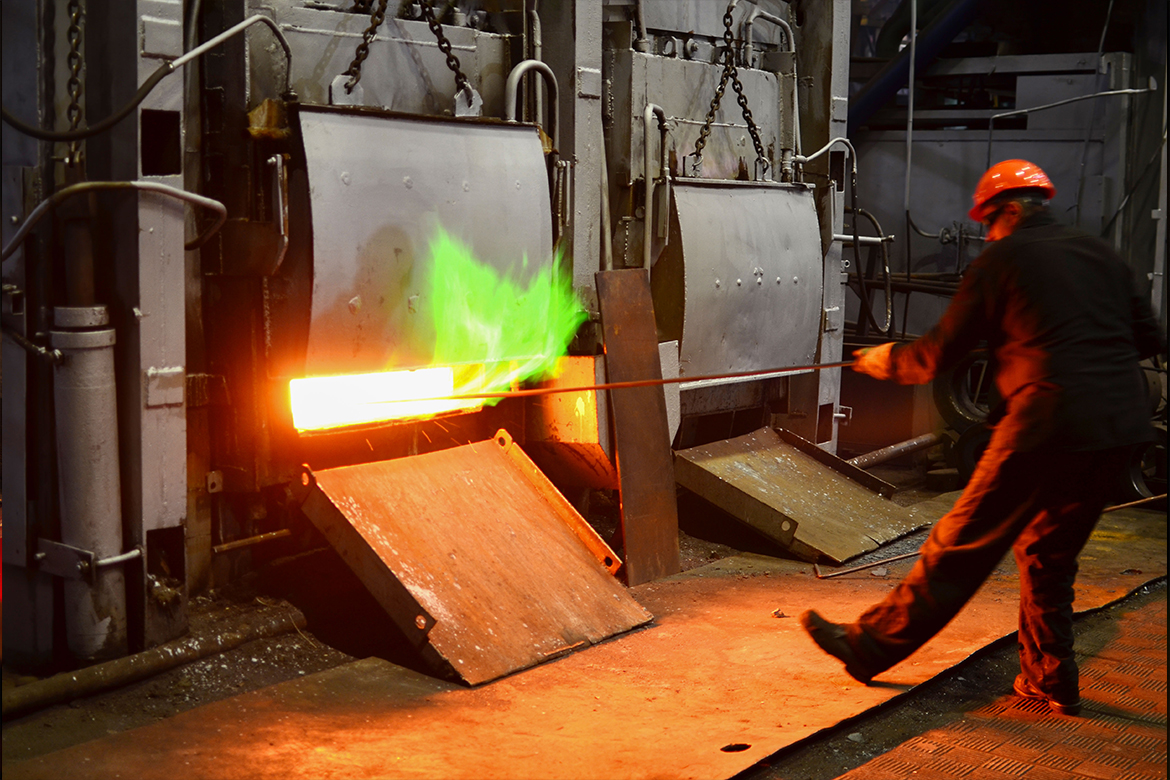
Il materiale presenta una struttura finale molto rigida e fragile dopo il processo di tempra e durante il raffreddamento istantaneo si creano delle tensioni interne. Pertanto, nel processo di rinvenimento, il matenale viene nuovamente riscaldato, mantenuto alla stessa temperatura per un certo periodo, e raffreddato per migliorarne la durezza.
Il processo di rinvenimento può essere eseguito a temperature diverse a seconda del tasso di tenacità, del valore di durezza e della struttura finale desiderati. Il rinvenimento di un pezzo che viene completamente raffreddato dopo il processo di tempra può causare fenomeni di fessurazione. Per questo motivo, il rinvenimento deve essere effettuato immediatamente quando la temperatura del pezzo in lavorazione scende in un intervallo compreso tra 60°C-80°C.
CEMENTAZIONE
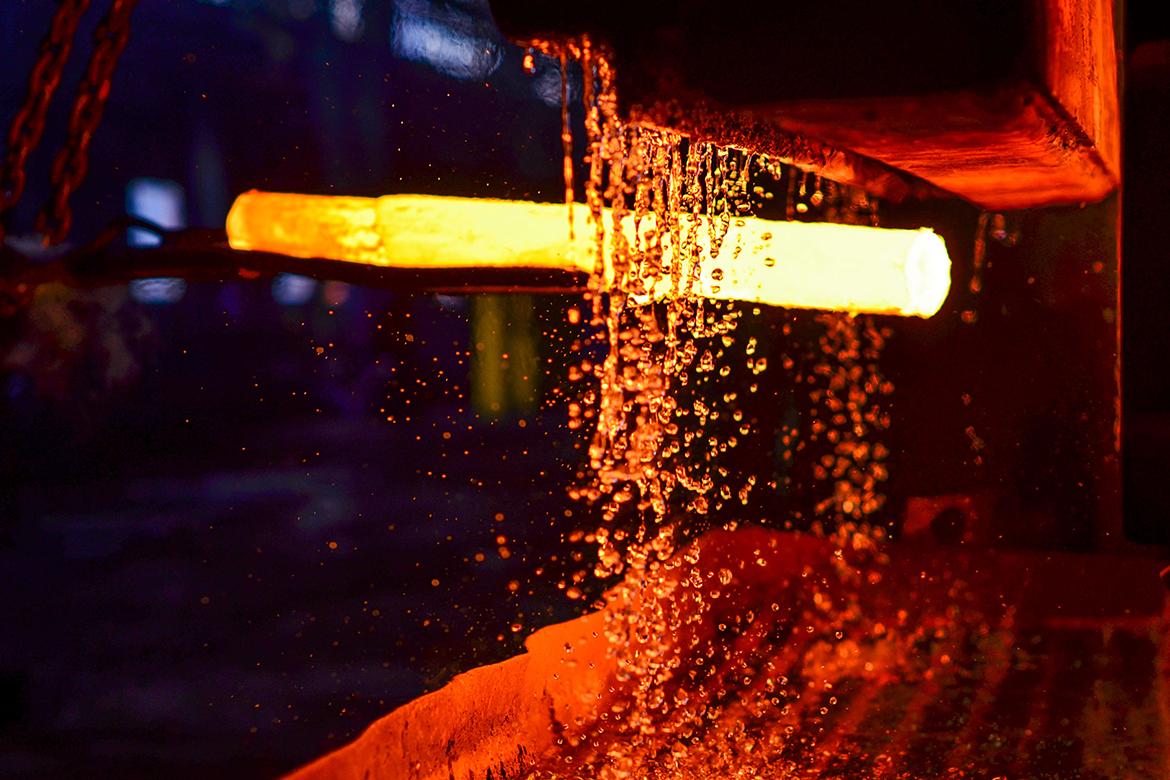
La lavorabilità meccanica dei materiali in acciaio a basso tenore di carbonio è molto elevata. Per questo motivo, in seguito al processo di lavorazione, essi vengono sottoposti al processo di tempra che apporta ulteriore carbonio in base agli usi cui sono destinati. Questo procedimento aumenta la resistenza all'usura della superficie del pezzo. Fornisce inoltre la necessaria tenacità e un'elevata resistenza all'urto all'intero pezzo, mantenendone morbida l'area del nucleo.
Il processo di cementazione può essere eseguito tramite un mezzo in fase solida, liquida o gassosa. La cementazione in un mezzo gassoso è l'ideale, in quanto è economica e rappresenta il metodo più semplice da controllare. Gli idrocarburi come il monossido di carbonio o il gas di carbone, ecc. sono utilizzati come mezzo di carbonizzazione. I sali carbonizzanti come il cianuro di sodio e il cianuro di potassio, ecc. sono ampiamente utilizzati nei processi di cementazione con un mezzo carbonizzante liquido. Il mezzo liquido è di solito preferito per il processo di cementazione di piccoli pezzi. Il carbone, invece, è ampiamente utilizzato come mezzo solido nei processi di cementazione. Dal momento che questo metodo è complesso e difficile da controllare, richiede competenza.
L'obiettivo del processo di cementazione è quello di aumentare il tasso di carbonio sulla superficie del pezzo dello 0,7-0,8%. Una quantità di carbonio superiore a questo intervallo porta a precipitazioni di carburo e si traduce in una superficie fragile. Il fattore critico nel processo di cementazione è la determinazione della profondità effettiva dello strato.
Il pezzo in lavorazione viene sottoposto ad un processo di tempra in seguito al processo di infusione di carbonio, quindi alla cementazione delle sue pareti. Il processo di tempra viene effettuato alla temperatura di infusione del carbonio (tempra diretta), il raffreddamento avviene a temperatura ambiente e il trattamento (tempra singola), o trattamento a bassa temperatura dopo la tempra, alla temperatura di infusione del carbonio. Il rinvenimento deve essere effettuato dopo il processo di tempra. La massima resistenza all'usura dopo il processo di cementazione può essere raggiunta con la tempra a circa 300°C piuttosto che al massimo valore di durezza.
TEMPRA AD INDUZIONE
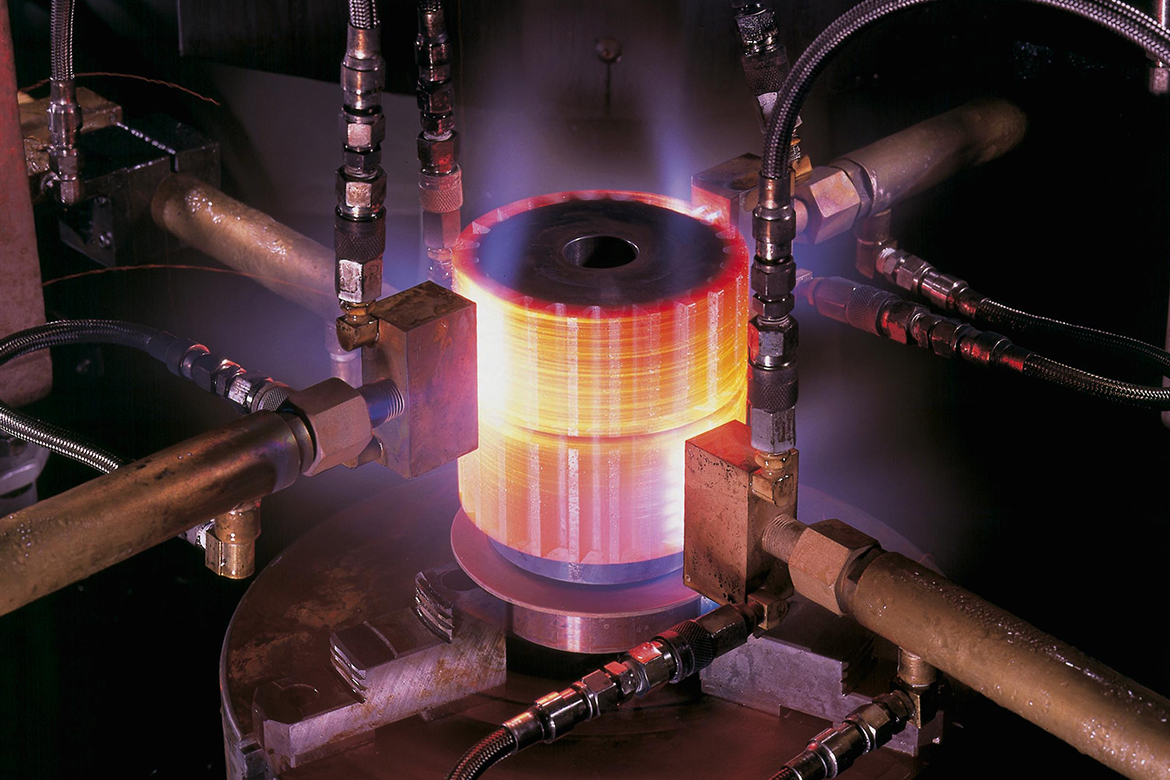
Il processo di tempra a induzione può essere definito come un processo di tempra superficiale in cui la superficie del pezzo viene riscaldata istantaneamente utilizzando correnti elettriche indotte e poi raffreddata istantaneamente mediante tempra. Sebbene il metodo sia simile alla tempra a fiamma, la tempra ad induzione offre vantaggi in termini di efficienza considerando la durata del processo e l'elevato accumulo termico sulla sua superficie. In genere il pezzo, dopo aver subito un riscaldamento istantaneo attraverso correnti indotte, viene raffreddato istantaneamente in acqua. Pertanto, il rischio di fessurazione aumenta negli acciai ad alto tenore di carbonio. Tuttavia, se la temperatura del mezzo di raffreddamento (acqua) è di circa 60°C o se si aggiunge il sale comune, il rischio di fessurazioni e di stress interno può essere eliminato.
Per evitare sollecitazioni interne, il processo di rinvenimento viene effettuato a una temperatura compresa tra 150 e 200 °C dopo il processo di tempra
We want to make our websites more user-friendly and continuously improve them. If you continue to use the websites, you agree to the use of cookies. OK For further information, please refer to our cookie policy...