Inspección y Pruebas
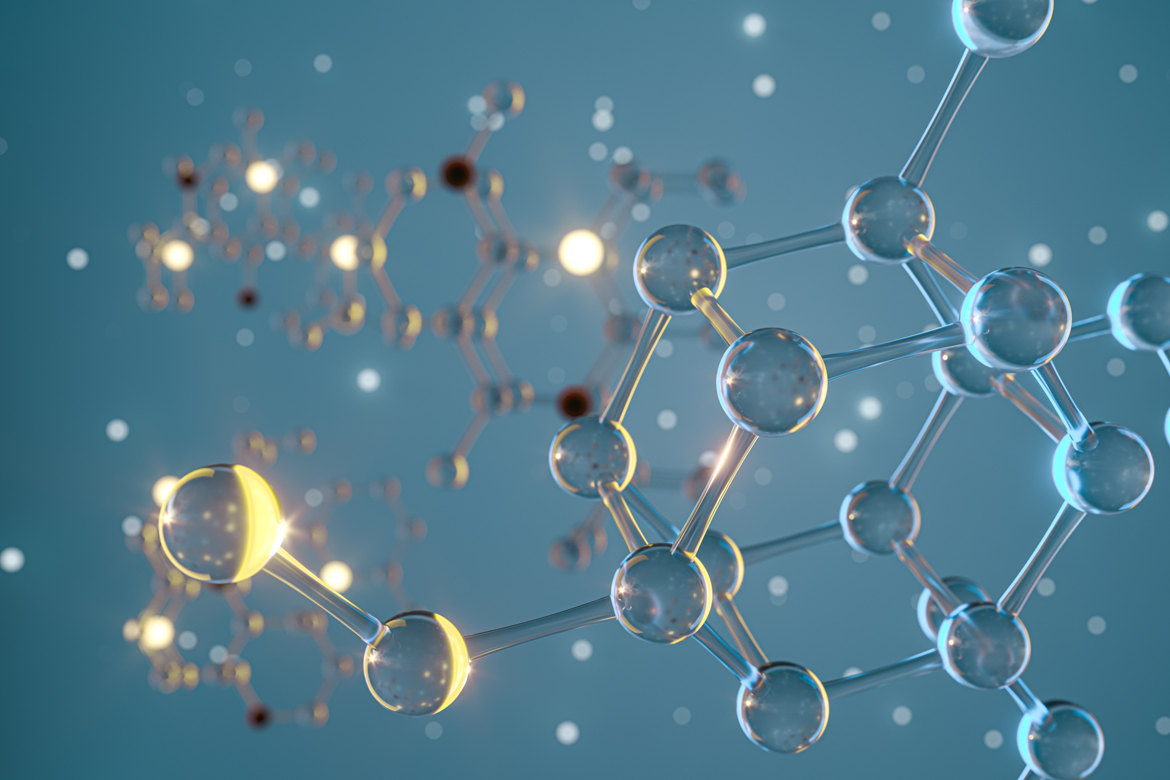
Para proporcionar continuamente el nivel de calidad requerido y la seguridad de un producto, es muy importante aplicar ciertos pasos de prueba e inspecciones en materias primas, componentes y ensamblajes de productos durante cada fase de los procesos de fabricación.
Como Turcont, seguimos ciertos estándares escritos de calidad, inspección y de prueba durante todas las etapas de fabricación, desde la adquisición del material hasta la entrega del producto final para verificar que se cumplan todos los requisitos especificados por el cliente.
Bajo la responsabilidad de esta división, brindamos los siguientes servicios a nuestros valiosos clientes:
- Adquisición e identificación de materiales, piezas y conjuntos y establecimiento de trazabilidad,
- Controles del proceso de producción y montaje.
- Validación de equipos subcontratados,
- Control de equipos suministrados por los clientes.
- Mantener registros de inspección y pruebas.
- Mantenimiento de equipos de prueba, inspección y medición
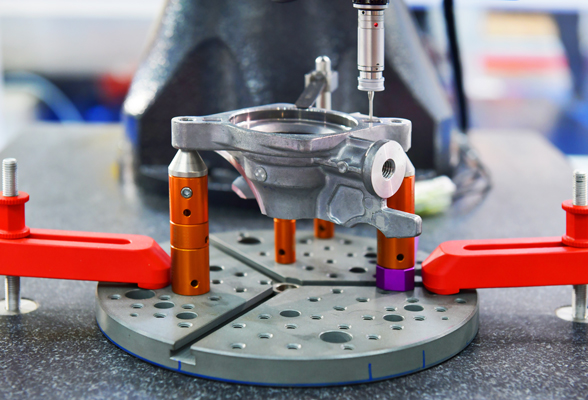
INSPECCIÓN DIMENSIONAL
El procedimiento de inspección dimensional analiza las características geométricas del material en bruto y de las partes maquinadas para validar el cumplimiento con las especificaciones de diseño. Este proceso de control confirma la exactitud de las características del producto que pueden afectar la confiabilidad y la funcionalidad.
Con nuestra experiencia y los equipos de medición de última tecnología que usamos, los clientes de Turcont reciben resultados de mediciones confiables de modo que puedan penetrar nuevos mercados sin dudar en la calidad. Esto les da una ventaja competitiva.
PRUEBAS DE MATERIALES
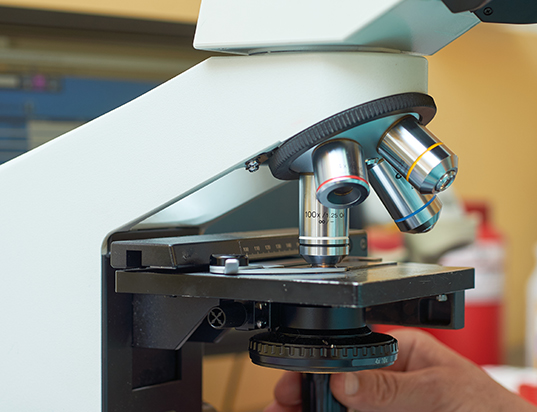
EXAMEN METALOGRÁFICO
El estudio microscópico de metales y sus aleaciones se denomina metalografía. Bajo este estudio, las propiedades microscópicas de los metales cambian al someterse a los diferentes procesos de manufactura, tales como: forja, fundición, soldadura, maquinado, recubrimiento y tratamiento térmico.
Los metales y sus aleaciones están formados por cristales llamados policristalinos o granos. Para comprender el uso del metal, la forma de fabricación y la historia de la producción del metal, el metalogógrafo examina la muestra observando la forma, el tamaño y la configuración de los granos.
El examen microestructural produce información cuantitativa sobre los siguientes criterios de la muestra:
- tamaño del grano
- distribución y cantidad de fases,
- área interfacial por unidad de volumen.
- dimensiones de las fases constituyentes
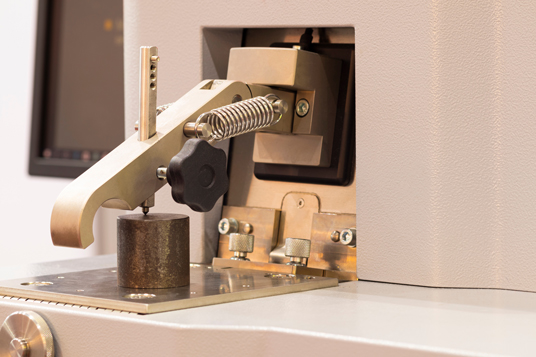
ANÁLISIS QUÍMICO
EL análisis químico es usado para descubrir la composición del material. Proporciona información acerca de los ingredientes, calidad y composición de los materiales usados en la fabricación del producto en cuestión.
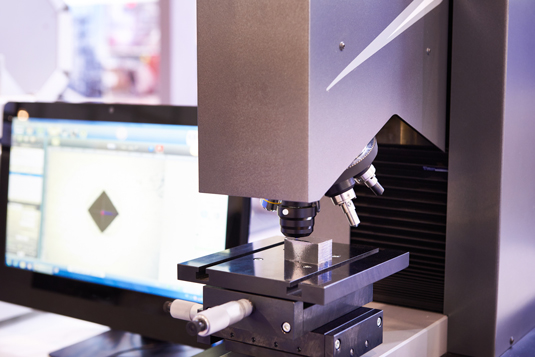
PRUEBA DE DUREZA
La prueba de dureza se define como la medida de la resistencia del material a la penetración. Si el material es duro, la resistencia a la penetración será mayor. Todo tiene que ver con las propiedades mecánicas del material. La dureza está influenciada por diversos factores, tales como el tamaño de grano, tensiones de endurecimiento, microestructura, etc.
Cuando la dureza incrementa, también incrementan el límite elástico y la resistencia a la ruptura (UTS por sus siglas en inglés) de modo que es necesario que las especificaciones incluyan la prueba de dureza en lugar de la prueba de tensión.
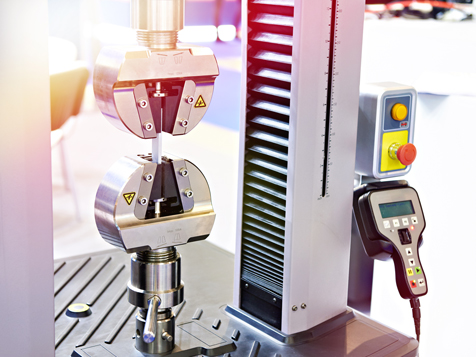
PRUEBA DE TENSIÓN
Entre las pruebas destructivas que se aplican a los materiales, la más importante es la prueba de tensión. Se lleva a cabo aplicando una fuerza de tracción a un material de modo que se pueda medir la respuesta de ña muestra a dicho estrés. Esto contribuye a conocer la resistencia del material ante el estiramiento.
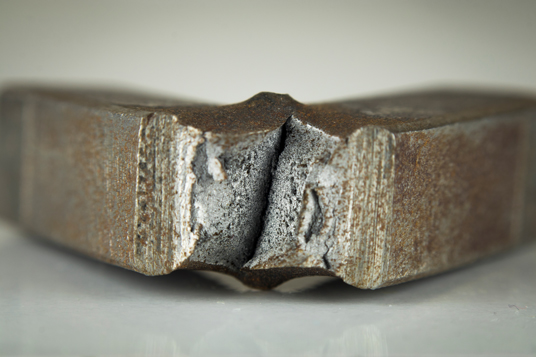
PRUEBAS DE IMPACTO
Esta prueba proporciona un método con carga rápida y que es adecuado para la propiedad de resistencia de un material o para determinar la tendencia a la fractura. Esta prueba no es para revelar los valores de las características del material.
La resistencia al impacto de la barra con muescas utilizada en la prueba de impacto nos ayuda sólo en la selección aproximada de • materiales para una tarea específica en lugar de calcular exactamente los valores de resistencia.
PRUEBAS NO DESTRUCTIVAS (PND)
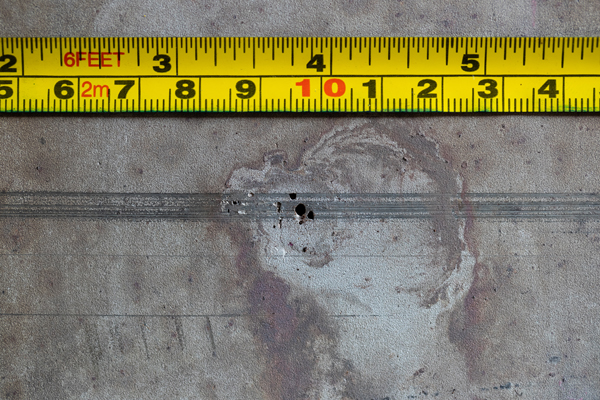
INSPECCİÓN VİSUAL (IV)
El objetivo principal de esta prueba original es el de detectar defectos de superficie tales como corrosión, alineado incorrecto de partes, daño físico y fisuras mediante la observación visual de la superficie. Se trata de la prueba no destructiva más efectiva.
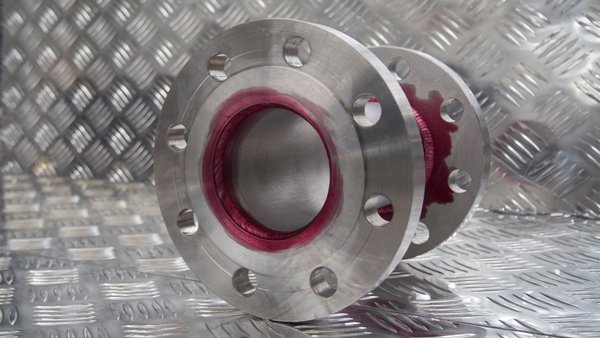
PRUEBA DE LÍQUIDO PENETRANTE (LP)
La prueba del líquido penetrante, también denominada prueba de tintes penetrantes, descubre grietas y poros superficiales mediante la práctica de fuerzas capilares para hacerlas visibles. Numerosos defectos de continuidad de superficie tales como porosidad, faldones y grietas pueden ser detectados con este método.
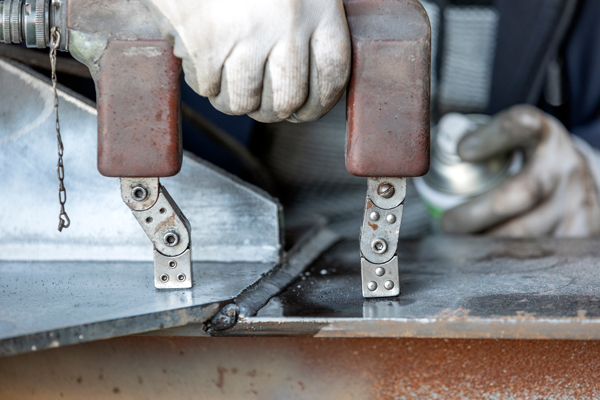
PRUEBA DE PARTÍCULAS MAGNÉTICAS
Este método de prueba es usado para detectar discontinuidades y defectos localizados en las superficies y en capas poco profundas subsuperficiales de hasta 2 mm de profundidad, que no son fácilmente identificables a simple vista.
Se lleva a cabo usando partículas ferromagnéticas bajo campos magnéticos en las áreas de inspección del material en prueba. El propósito es decubrir el defecto por la presencia de una fuga del flujo del campo. Estas partículas ferromagnéticas se aplican suspendidas en un líquido o en aire.
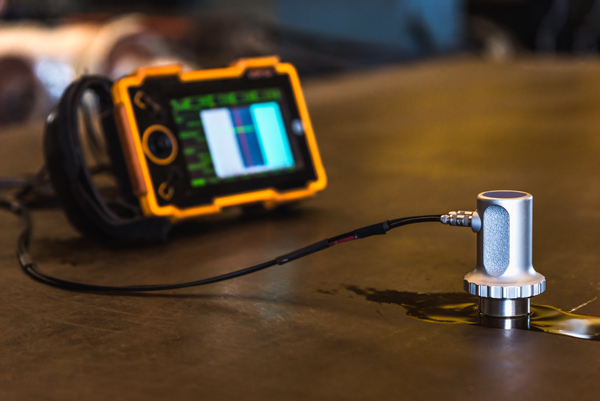
PRUEBAS ULTRASÓNICAS (PU)
La inspección ultrasónica es una prueba crucial para componentes relevantes en la seguridad. Los problemas invisibles y las heterogeneidades enmascaradas se pueden descubrir y localizar aplicando esta prueba. También proporciona mediciones de espesor de pared además de la detección de fallas.
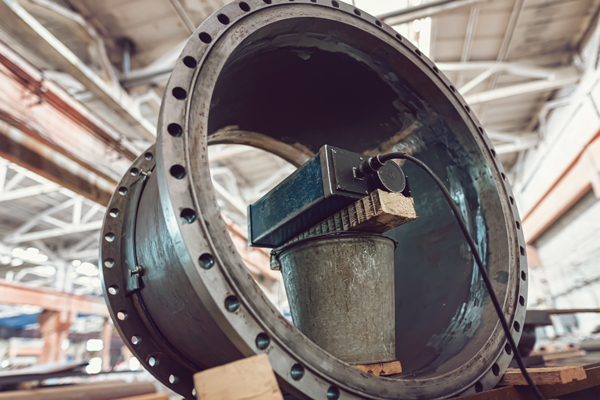
PRUEBAS RADIOGRÁFICAS (PR)
Esta prueba usa ya sea rayos gamma o rayos X para ver el interior de un componente. Se utiliza para descubrir fallas en recipientes a presión y válvulas en la industria petroquímica. También se usa en la inspección de reparaciones por soldadura.
PR ofrece varias ventajas en comparación con otras técnicas no destructivas. Éstas son;
- no requiere demasiada preparación de la superficie.
- fácil de usar en el campo y en posiciones elevadas gracias a su portabilidad.
- se puede utilizar en una variedad de materiales,
- Los datos recopilados se pueden guardar para un análisis posterior.
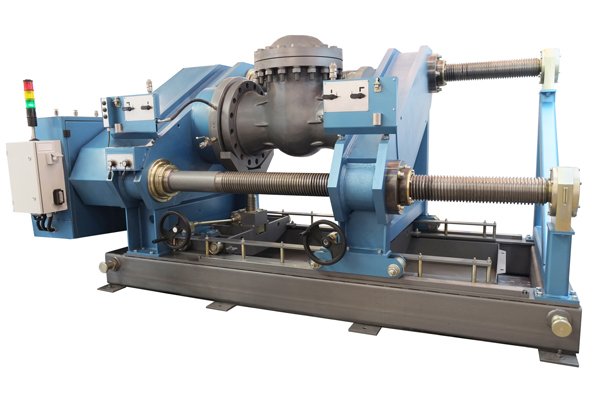
PRUEBA HIDROSTÁTICA
Al aplicar este método, la continuidad de los recipientes es probada bajo presión para descubrir fugas, demostrando la fuerza y validando el desempeño.
La prueba hidrostática es uno de los ensayos no destructivos, sin embargo, si ocurre una falla y la pieza no cumple con las especificaciones de durabilidad o de desempeño, el recipiente quedará inutilizado.
Cuando/después de aplicar esta prueba, hay varios indicadores que muestran una calidad inadecuada del recipiente. Estos son:
- fugas a través del producto y malformaciones.
- una disminución de la presión aplicada,
- abultamiento o distorsión en el product
We want to make our websites more user-friendly and continuously improve them. If you continue to use the websites, you agree to the use of cookies. OK For further information, please refer to our cookie policy...